What impacts the cost of an architectural and custom scale models?
- Tom Price
- Sep 8, 2020
- 4 min read
Updated: Sep 20, 2020
Probably the biggest question in our business is how are models priced? Well its not an easy answer but here is the theory behind scale modeling costs. This is true of Titanic Design and model making in general. Like most enterprises creating models roughly follows the iron triangle of project management. Or perhaps in our case the iceberg of reality
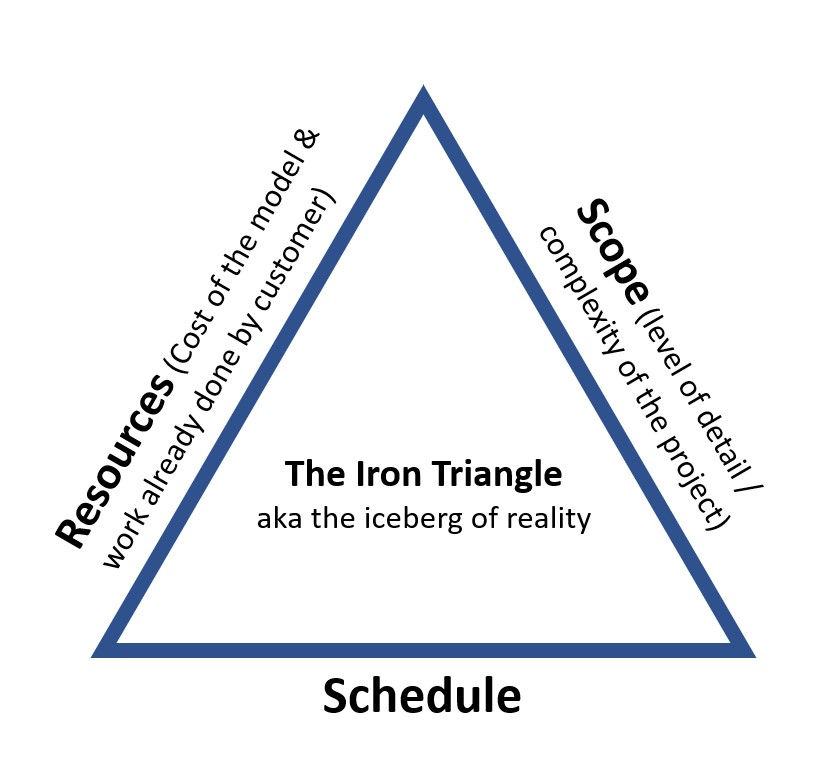
A project is defined by its resources (Cost of the model & work already done by customer*), scope (level of detail / complexity of the project), and schedule. Fast high quality projects are possible but they require close coordination with clients and cost more. See how we created a site model for a futuristic middle eastern city in 10 days.
*A high quality technical documents & CAD package provided to our team
Custom modeling projects consist of two phases that have to occur in series.
I. Model preparation & planning
II. Physical model creation
Model preparation is usually the most expensive part of creating a physical model. Typically this ranges anywhere from 50%-85% of a project's cost. This is broken down into several sub-steps:

1. Reviewing customer documents
In this stage selected members of our team who will be quoting and then executing a project need to get up to speed and understand as much as possible about the project quickly and then understand the request & goals of a model. The more information you have the better, delivering a comprehensive package helps us help you. While we can and have worked from just pictures or an address and made large complex site models and from full engineering CAD packages. The more documentation you can provide us with the better we can understand your project and save time. The process can be sped along and helped the most by reviewing our list of questions that we ask potential architectural and custom scale model clients.

2. Exporting into a working format.
After we have understood a project and developed requirements we then need to take whatever documentation exists and pull it into a useful format for our team to most easily work with. If you have an architectural/engineering CAD software we can work with you to export it into the most useful formats for starting our work. See our article on file formats most useful for our work. This portion of the process can be reduced by already having high quality architectural CAD data from a reputable CAD package such as Revit or Rhino. Other architectural CAD software can also be helpful. And if necessary we can use .pdfs, physical plans, or even pictures.

3. Modeling preparation & developing manufacturing plan
Leveraging what artifacts we have our team goes about designing the pieces we will use to create a model for our customer. This may be remodeling components or structures for 3D printing, developing laser cut paths, or just planning out what we are going to make the old fashioned way. At this stage we will review our plan and require any unique items also needed for a model such as unique facade materials or custom scale components. This stage can be reduced by again providing high quality or even 3D print ready CAD files and reducing details that require high manual labor that cannot be automated. Our team will discuss options here.
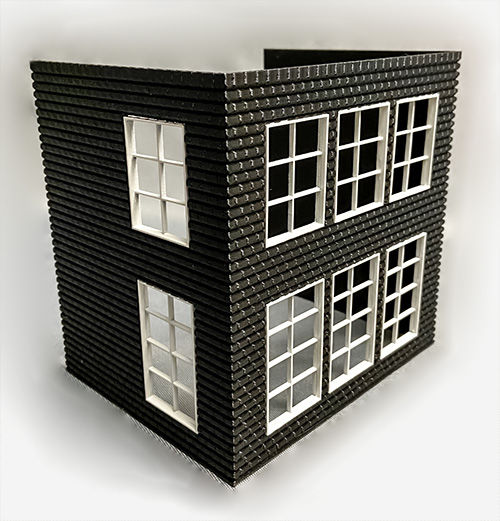
4. Concept testing (if necessary) For complex or unique components on a project our team will perform small tests to ensure any risks are addressed. This may be testing a custom blend of flocking to make sure it works well at the architectural scale or ensuring a custom feature such as a laser engraved facade behaves as expected. At this stage a final digital model will be presented to a customer for review when necessary. With approval we begin physical model creation. Physical model creation
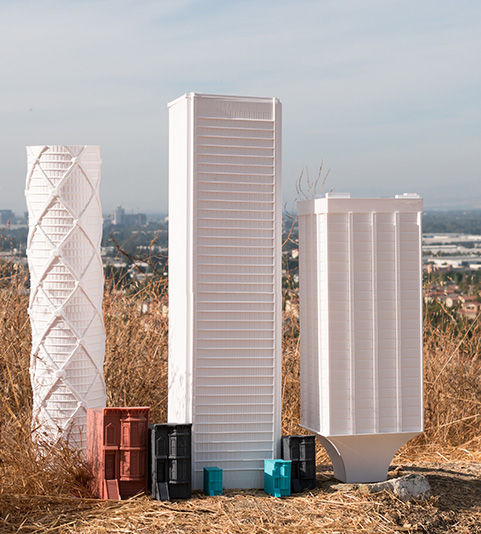
After preparation is completed physical work begins. Titanic Design leverages advanced manufacturing and 3D printing while blending in traditional model making techniques and craftsmanship. This allows us to provide amazing value to our customers. As a result this stage is usually quick. However big factors increase our and every model makers physical model creation time and cost. High detail elements (people, cars, high detail foliage, lighting, moving parts) add life to a model. Adding this character to a model can create an amazing piece and a new dimension of depth. However this work can't be automated and simply takes human time to carefully and thoughtfully place these pieces. See our Tech Data Center, Villa Rio luxury apartments, or vertical farming prototype to see some of these elements at play.
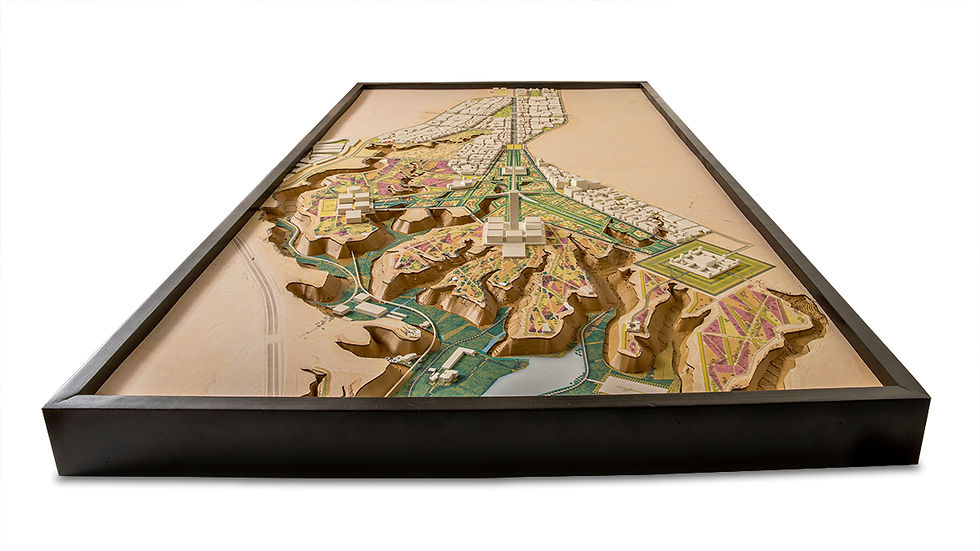
A base for a model is also a key cost. In some cases (such as incorporating high detail elements) a base is all but required but in other projects it may not be needed. We have a whole article discussing bases

Focusing on advanced technology and fabrication lets us save and tweak designs. Multiple models can be easily made even with high detail elements. As a large project progresses and evolves during its design phase models can be rebuilt. However changes also come at a cost. We create models fairly quickly. If we are made aware of these incoming possibilities at the start of a project they can be planned for and mitigated. See how we made hundreds of custom scale stack-able buildings for a cities major redevelopment effort that could be configured as their project evolved. Or this interior apartment layout rapidly digitally generated and made leveraging our CNC fabrication equipment. If you understand some of the factors impacting cost of a model making its also good to understand the other factors more broadly as we scope out a model project. See the questions you should ask yourself, before we do, in the anatomy of an architectural and modeling quote.
If you are ready then reach out to us on our contact page!
Comments